Basic Materials Guide
Disclaimer: The data furnished herein is based on years of experience, testing and our vendors engineering information. All reasonable care has been taken to ensure the accuracy of the contents of this material; however, Harrington Industrial Plastics LLC shall not be liable or responsible for any loss whether direct, indirect, incidental or consequential arising out of the use of or reliance upon any of the contents of this material.
POLYVINYLS
PVC (POLYVINYL CHLORIDE) has a relatively high tensile strength and modulus of elasticity and therefore is stronger and more rigid than most other thermoplastics. The maximum service temperature of PVC is 140°F for Type 1. PVC has excellent chemical resistance to a wide range of corrosive fluids but may be damaged by ketones, aromatics, and some chlorinated hydrocarbons. It has proved an excellent material for process piping (liquids and slurries), water service, and industrial and laboratory chemical waste drainage. Joining methods are solvent welding, threading (Schedule 80
only), or flanging.
CPVC (CHLORINATED POLYVINYL CHLORIDE) is particularly useful for handling corrosive fluids at temperatures up to 210°F. In chemical resistance, it is comparable to PVC. It weighs about one-sixth as much as copper, will not sustain combustion (self-extinguishing), and has low thermal conductivity. Suggested uses include process piping for hot, corrosive liquids; hot and cold water lines in office buildings and residences; and similar applications above the temperature range of PVC. CPVC pipe may be joined by solvent welding, threading, or flanging.
POLYOLEFINS
POLYPROPYLENE (HOMOPOLYMER) is the lightest thermoplastic piping material, yet it has considerable strength, outstanding chemical resistance, and may be used at temperatures up to 180°F in drainage applications. Polypropylene is an excellent material for laboratory and industrial drainage piping where mixtures of acids, bases, and solvents are involved. It has found wide application in the petroleum industry where its resistance to sulfur- bearing compounds is particularly useful in salt water disposal lines, chill water loops, and demineralized water. Joining methods are coil fusion and socket heat welding.
COPOLYMER POLYPROPYLENE is a copolymer of propylene and polybutylene. It is made of high molecular weight copolymer polypropylene and possesses excellent dielectric and insulating properties because of its structure as a nonpolar hydrocarbon polymer. It combines high chemical resistance with toughness and strength at operating temperatures from freezing to 200°F. It has excellent abrasion resistance and good elasticity, and is joined by butt and socket fusion.
POLYETHYLENE is generally described in three classifications according to the relative degree of branching (side chain formation) in their molecular structures and density. Low Density Polyethylene (LDPE) has more extensive branching resulting in less compact molecular structures and lower mechanical strength than other Polyethylenes. Good for temperatures to 140°F and is frequently used for food handling equipment, brine tanks and dispensing equipment. It may be hot gas welded if required.
High Density Polyethylene (HDPE) has minimal branching, which makes it more rigid and less permeable than LDPE. It is good for temperatures to 160°F and is frequently used for abrasion resistant piping, caustic storage tanks, and control tubing. It may be hot gas welded. Cross-Linked High Density Polyethylene (XLPE) is a three-dimensional polymer of extremely high molecular weight with individual molecular chains bonded together using heat plus chemicals or radiation. This structure provides superior environmental stress-crack resistance and extremely high impact strength. Cross-linked Polyethylene becomes a thermoset material after manufacturing and cannot be hot gas welded. Good for temperatures to 160°F with most common uses including large tanks for outdoor service. All polyethylene has excellent chemical resistance to a wide range of common chemicals. Avoid strong oxidizing agents and solvents.
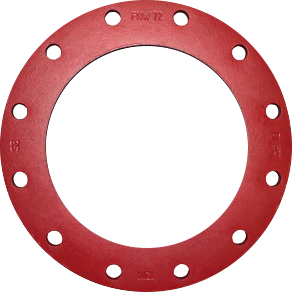
FLUOROPOLYMERS
TEFLON – There are three members of the Teflon family of resins:
- PTFE TEFLON is the original Teflon resin developed by DuPont in 1938. This fluoropolymer offers the most unique and useful characteristics of all plastic materials. Products made from this resin handle liquids or gases up to 500°F. The unique properties of this resin prohibit extrusion or injection molding by conventional methods. When melted, PTFE does not flow like other thermoplastics and it must be shaped initially by techniques similar to powder metallurgy. Normally PTFE is an opaque white material. Once sintered it is machined to the desired part.
- FEP TEFLON was also invented by DuPont and became a commercial product in 1960. FEP is a true thermoplastic that can be melt-extruded and fabricated by conventional methods. This allows for more flexibility in manufacturing. The dielectric properties and chemical resistance are similar to other Teflons, but the temperature limits are -65°F to a maximum of 300°F. FEP has a glossy surface and is transparent in thin sections. It eventually becomes translucent as thickness increases. FEP Teflon is the most transparent of the three Teflons. It is widely used for its high ultraviolet light–transmitting ability.
- PFA TEFLON, a close cousin of PTFE, was introduced in 1972. It has excellent melt process ability and properties rivaling or exceeding those of PTFE Teflon. PFA permits conventional thermoplastic molding and extrusion processing at high rates and also has higher mechanical strength at elevated temperatures to 500°F. Premium grade PFA Teflon offers superior stress and crack resistance with good flex-life in tubing. It is generally not as permeable as PTFE.
Caution: While the Teflon resin family has great mechanical properties and excellent temperature resistance, care must be taken when selecting the proper method of connections for your piping system. Generally, Teflon threaded connections will handle pressures to 120 psig. Loose ferrule connections are limited to 60 psig at ambient temperatures. Teflon loses its ability to bear a load at elevated temperatures quicker than other thermoplastics. When working with the PTFE products shown in this catalog. External ambient temperatures ranging from -60°F to 250°F (-51°C to 121°C) may be handled safely. Fluid or gas temperatures inside the product should be limited to -60°F to 400°F (-51°C to 204°C) unless otherwise noted.
Always use extreme care when working with chemicals at elevated temperatures.
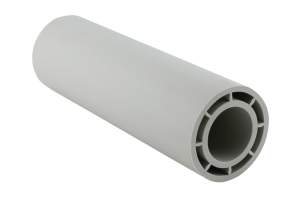
DURAPLUS
ABS (ACRYLONITRILE-BUTADIENE-STRENE) There are many possibilities for polymer properties by combining these resins.
- The less expensive ABS resin is used in drain, waste, and vent applications.
- The other is used for more stringent industrial applications has a different combination of the three polymers that make up the copolymer. The Duraplus product is made from this copolymer and has outstanding impact resistance even at low temperatures. The product is very tough and abrasion resistant. Temperature range is -40°F to 158°F.
RYTON (PPS) POLYPHENYLENE SULFIDE remains quite stable during both long and short term exposure to high temperatures. The high tensile strength and flexural modulus typical of PPS compounds decrease with an increase in temperature. PPS is also highly resistant to chemical attack. Relatively few chemicals react to this material even at high temperatures. Its broad range of chemical resistance is second only to that of Teflon (PTFE). Ryton is used primarily for precision pump parts.
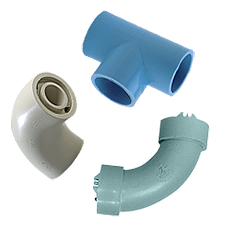
ELASTOMERS
VITON (FLUOROCARBON) is inherently compatible with a broad spectrum of chemicals. Because of this extensive chemical compatibility which spans considerable concentration and temperature ranges, Viton has gained wide acceptance as a sealant for valves, pumps, and instrumentation. Viton can be used in most applications involving mineral acids, salt solutions, chlorinated hydrocarbons, and petroleum oils.
EPDM (EPT) is a terpolymer elastomer made from ethylenepropylene diene monomer. EPDM has good abrasion and tear resistance and offers excellent chemical resistance to a variety of acids and alkalies. It is susceptible to attack by oils and is not recommended for applications involving petroleum oils, strong acids, or strong alkalies.
HYTREL is a multi-purpose polyester elastomer similar to vulcanized thermoset rubber. Its chemical resistance is comparable to Neoprene, Buna-N and EPDM; however, it is a tougher material and does not require fabric reinforcement as do the other three materials. Temperature limits are -10°F minimum to 190°F maximum. This material is used primarily for pump diaphragms.
THERMOSETS
FIBERGLASS REINFORCED PLASTICS (FRP) including epoxy, polyester, and vinylester have become a highly valuable process engineering material for process piping. FRP has been accepted by many industries because it offers the following significant advantages: (a) moderate initial cost and low maintenance; (b) broad range of chemical resistance; (c) high strength-to-weight ratio; (d) ease of fabrication and flexibility of design; and (e) good electrical insulation properties.
EPOXY pipe and fittings have been used extensively by a wide variety of industries since 1960. It has good chemical resistance and excellent temperatures to pressure properties (to 300°F). Epoxy has been used extensively for fuel piping and steam condensate return lines.
POLYESTER pipe and fittings have been used by the industry since 1963. They have proven resistance to most strong acids and oxidizing materials. They can be used in applications up to 200°F. Polyester is noted for its strength in both piping and structural shapes.
VINYLESTER resin systems are recommended for most chlorinated mixtures as well as caustic and oxidizing acids up to 200°F. For most services, Vinylester has superior chemical resistance to epoxy or polyester.
NYLONS are synthetic polymers that contain an amide group. Their key characteristics are: (a) excellent resistance and low permeation to fuels, oils, and organic solvent, including aliphatic, aromatic, and halogenated hydrocarbons, esters, and ketones; (b) outstanding resistance to fatigue and repeated impact; and (c) wide temperature range from -30°F to 250°F.
Caution: Acids will cause softening, loss of strength, rigidity, and eventual failure.
POLYURETHANES – There are essentially two types of polyurethanes: polyester based and polyether based. Both are used for tubing applications:
- POLYESTER-based is the toughest of the two, having greater resistance to oil and chemicals. It does not harden when used with most oils, gasoline, and solvents. Polyurethane is extremely resistant to abrasives making it ideal for slurries, solids, and granular material transfer. Temperature limit is 170°F.
Caution: Polyester-based polyurethanes may be subject to hydrolysis under certain conditions, high relative humidity at elevated temperatures, aerated water, fungi, and bacteria. Where these potentials exist, we recommend polyether-based polyurethane..
- POLYETHER-based polyurethane possesses better low temperature properties, resilience, and resistance to hydrolytic degradation than the polyester previously discussed. Accelerated testing indicates that polyether-based polyurethanes have superior hydrolytic stability as compared to polyester-based material. Made with no plasticizers and with a low level of extractables, polyether is ideal for high-purity work. It will not contaminate laboratory samples and is totally non-toxic to cell cultures. Compared with PVC tubing, polyurethanes have superior chemical resistance to fuels, oils, and some solvents. Its excellent tensile strength and toughness make it suitable for full vacuums. This tubing can withstand temperatures from -94°F to 200°F.
PTBP Polybutylene Terephthalate is a little-known specialty material belonging to the polyimide group. It has excellent mechanical properties and good mechanical stress properties under corrosive environments. PTBP is used mainly for valve actuators and bonnet assembly.
Do you need to talk to an expert?
Call our toll-free number at 1-800-213-4528 and you will be connected to a live person – not a recording.
You may also use the contact form below for any questions regarding the products and brands we carry.