Basic Joining Techniques
Disclaimer: The data furnished herein is based on years of experience, testing and our vendors engineering information. All reasonable care has been taken to ensure the accuracy of the contents of this material; however, Harrington Industrial Plastics LLC shall not be liable or responsible for any loss whether direct, indirect, incidental or consequential arising out of the use of or reliance upon any of the contents of this material.
There are several recommended methods of joining thermoplastic pipe and fittings, each with its own advantages and limitations:
SOLVENT CEMENTING
The most widely used method in Schedule 40 PVC, Schedule 80 PVC and CPVC piping systems as described in ASTM D-2855. The O.D. of the pipe and the I.D. of the fitting are primed, coated with special cement and joined together. Knowledge of the principles of solvent cementing is essential to an excellent job.
NOTE: The single most significant cause of improperly or failed solvent cement joints is lack of solvent penetration or inadequate primer application.
There are various methods to join pipe and fittings when installing chlorinated polyvinyl chloride (CPVC) piping systems. One of the most common ways of joining is by solvent cementing. Solvent cement is not a glue — it is a process that uses solvents and resin to chemically fuse the pipe and fitting together at a molecular level.
Article: Solvent Cementing CPVC – The Dos and Don’ts of CPVC Piping Solvent Cement Welding – Corzan (External Link)
Article: Solvent Cementing CPVC – The Complete CPVC Solvent Cement Guide – Corzan (External Link)
THREADING
Schedule 80 PVC, CPVC, PVDF, and PP can be threaded with special pipe dyes for mating with Schedule 80 fittings provided with threaded connections. Since this method makes the piping system easy to disassemble, repair, and test, it is often employed on temporary or take-down piping systems, as well as systems joining dissimilar materials. Threaded pipe must be derated by 50% from solvent-cemented systems.
NOTE: Threaded joints are not recommended for PP pressure applications.
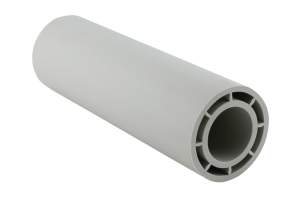
FLANGES
This technique is used to assemble PVDF and polypropylene pipe and fittings for high-temperature, corrosive-service applications. (See each manufacturer’s data for recommended joining techniques.)
SOCKET FUSION
This technique is used to assemble PVDF and polypropylene pipe and fittings for high-temperature, corrosive-service applications.
NOTE: See each manufacturer’s data for recommended joining techniques.
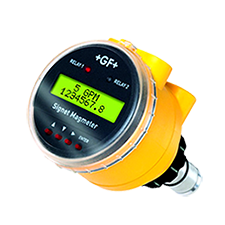
BUTT FUSION
IR (INFRARED)
HPF Fusion
SMOOTH INNER BORE (S.I.B.)
S.I.B. offers state-of-the-art technology for sanitary piping systems construction. The “smooth” interior surface of the weld eliminates all beads, crevices and intrusions into the fluid system. Materials cannot become entrapped, and the possibility of bacterial growth and contamination is virtually eliminated. S.I.B. reduces pressure loss due to friction and improves system hydraulics. Available in Kynar® (PVDF) and polypropylene.